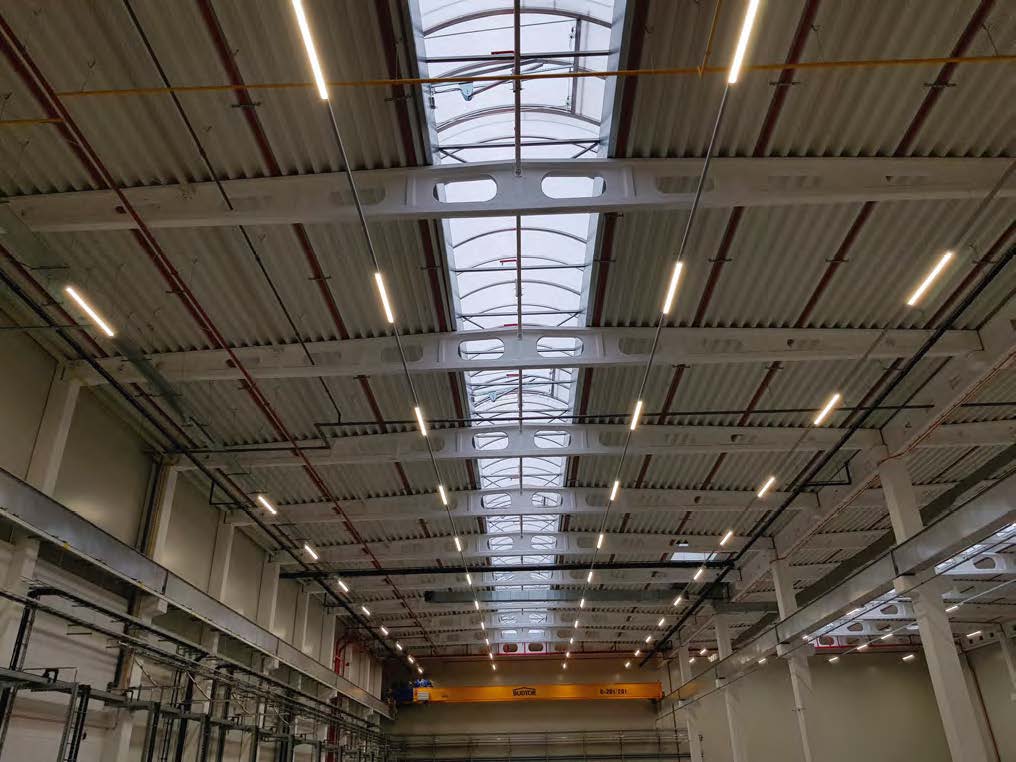
W związku ze zmieniającymi się trendami, a także łatwiejszym dostępem do nowych technologii oraz tańszych materiałów również obiekty przemysłowe – logistyczno-magazynowe i produkcyjne – można budować w tradycyjnym układzie konstrukcyjnym mieszanym (stal, beton) lub prefabrykowanym żelbetowym.
W większości obiektów logistyczno-magazynowych oraz produkcyjnych stosuje się technologię tradycyjną, tj. prefabrykowane żelbetowe słupy i podwaliny oraz stalową konstrukcję dachu (fot. 1.) Innym rozwiązaniem jest zastosowanie kompletnej prefabrykowanej żelbetowej konstrukcji dla słupów i podwalin oraz dachu (fot. 2.). Przyjęcie tego rozwiązania wiąże się z nieco innym podejściem do realizacji, zarówno na etapie projektowania, jak i wykonawstwa, oraz niesie ze sobą wiele korzyści (ale ma także swoje minusy). Wyzwaniem jest utrzymanie kosztów na zbliżonym poziomie w stosunku do tradycyjnego układu konstrukcyjnego, przez co projekt jest bardziej wymagający, ale i ciekawszy w realizacji. Z reguły wykonawcy wybierają tradycyjny układ konstrukcji (słupy żelbetowe + stalowa konstrukcja dachu) ze względu na różnicę w kosztach – wariant tradycyjny teoretycznie jest tańszy. Jest to również rozwiązanie stosowane przez większość firm podwykonawczych, co nie pozostaje bez znaczenia w przypadku ogromnego popytu na naszym rynku na ten segment budownictwa.

Optymalizacja z BIM
W optymalizacji kosztów pomaga na przykład zaprojektowanie obiektu w technologii BIM. Dzięki temu koordynacja branży konstrukcyjnej i instalacyjnej pozwala uniknąć wielu kolizji na etapie realizacji. W latach 2017–2018 popyt na elementy prefabrykowane oraz przejęcia istniejących zakładów przez firmy wykonawcze ograniczały możliwość uzyskania porównywalnych poziomów cenowych dla obu rozwiązań (jest znacznie więcej zakładów wytwarzających konstrukcje stalowe niż prefabrykowane żelbetowe sprężone). Rok 2019 ustabilizował rynek, powstało też kilka nowych zakładów wytwarzających prefabrykaty żelbetowe. Średni czas realizacji tych obiektów to 6–8 miesięcy (na błędy nie ma zbyt dużo miejsca), więc wybierając to rozwiązanie, trzeba przeanalizować wiele czynników, m.in. koszty i dostępność.
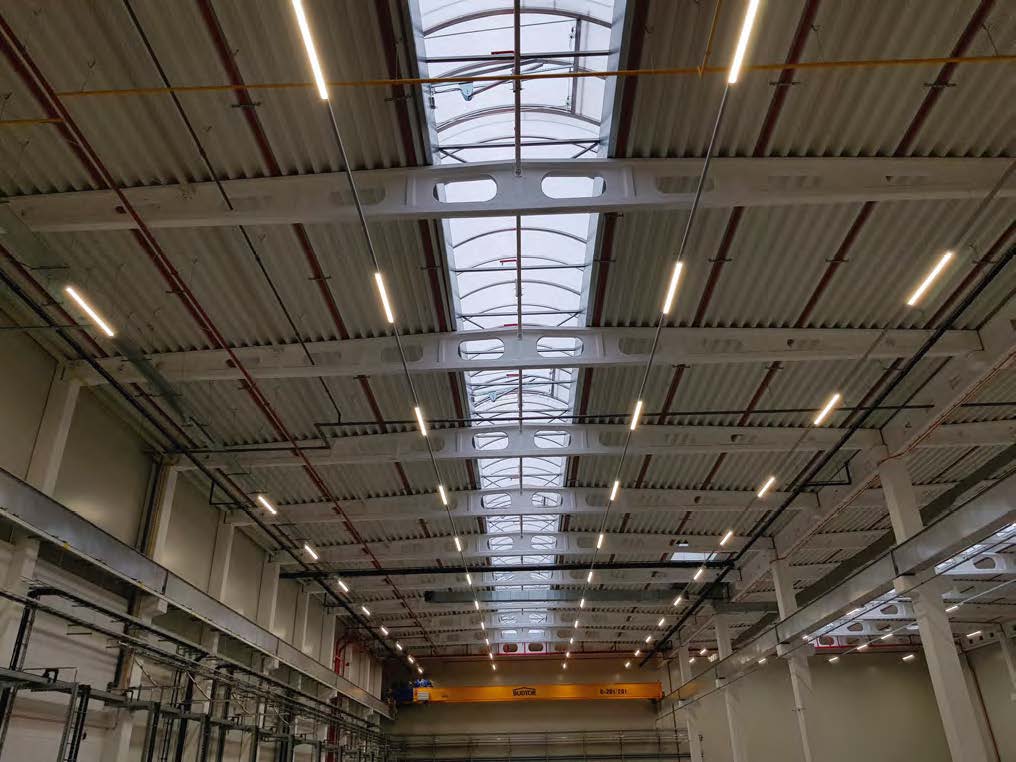
Ekologicznie…
Standardem przy tych obiektach staje się wymóg oceny budynków pod kątem ich ekologiczności i uzyskanie certyfikatu np. BREEAM, co kilka lat temu nie było takie oczywiste i zarezerwowane raczej dla budynków biurowych. Inteligentne dachy, takie jak system monitorowania ugięć konstrukcji dachu, to również rozwiązanie, które coraz częściej pojawia się przy omawianych realizacjach.
…i innowacyjnie
Z dodatkowych innowacji, które zostały użyte podczas realizacji jednego z naszych projektów dla wiodącego dewelopera z sektora magazynowo-logistycznego, można przywołać zastosowanie narzędzi w postaci aplikacji „bluebeem” (oprogramowanie służące do tworzenia i edytowania plików pdf), która świetnie współpracuje z plikami pakietu Microsoft Office, oraz aplikacji „aproplan”, używanej na etapie odbiorów, do identyfikacji usterek. Testowaliśmy również narzędzie do inteligentnego zarządzania logistyką na budowach. Przy optymalizacji robót ziemnych zostały wykorzystane pomiary geodezyjne przy użyciu dronów.
Korzyści wynikających z zastosowania elementów konstrukcyjnych dachu w technologii prefabrykowanej (przy zbliżonych kosztach) jest wiele. Osiągnęliśmy między innymi minimalną wysokość w świetle konstrukcji (od posadzki do spodu dźwigara) na poziomie 10,5–10,9 m względem standardowych wymagań – 10 m dla obiektów magazynowych, bez zmiany maksymalnej wysokości hali w attyce 12,3 m, co niewątpliwie podnosi wartość obiektu dla inwestora (większa przestrzeń magazynowania), dodatkowo konstrukcja prefabrykowana została wykonana w odporności ogniowej REI 60, co może mieć duże znaczenie dla obniżenia kosztów ubezpieczenia obiektu, jak również podwyższenia standardów w zakresie ppoż. Coraz częściej pojawia się także temat przygotowania konstrukcji obiektów pod montaż paneli fotowoltaicznych, co przy zastosowaniu wyżej wymienionego rozwiązania nie podniesie znacząco kosztów. Minusem zastosowania dźwigarów strunobetonowych w stosunku do typowej kratownicy stalowej jest otworowanie i możliwość przeprowadzenia instalacji w każdym kierunku. Dlatego też przy realizacji wspomnianego obiektu zostały zaprojektowane dźwigary sprężone „ażurowe”, a technologia BIM pozwoliła skoordynować wielkości oraz kształt otworów z przebiegiem instalacji. Zastosowanie opisanych powyżej, ciekawych i dostępnych rozwiązań pozwala uniknąć rutyny przy projektowaniu obiektów logistyczno-magazynowych i produkcyjnych, sprawiając, że powstające budynki są ciekawsze, bardziej ekonomiczne i innowacyjne – z oczywistą korzyścią dla inwestora.
Zdjęcia arch. CFE Polska Sp. z o.o.