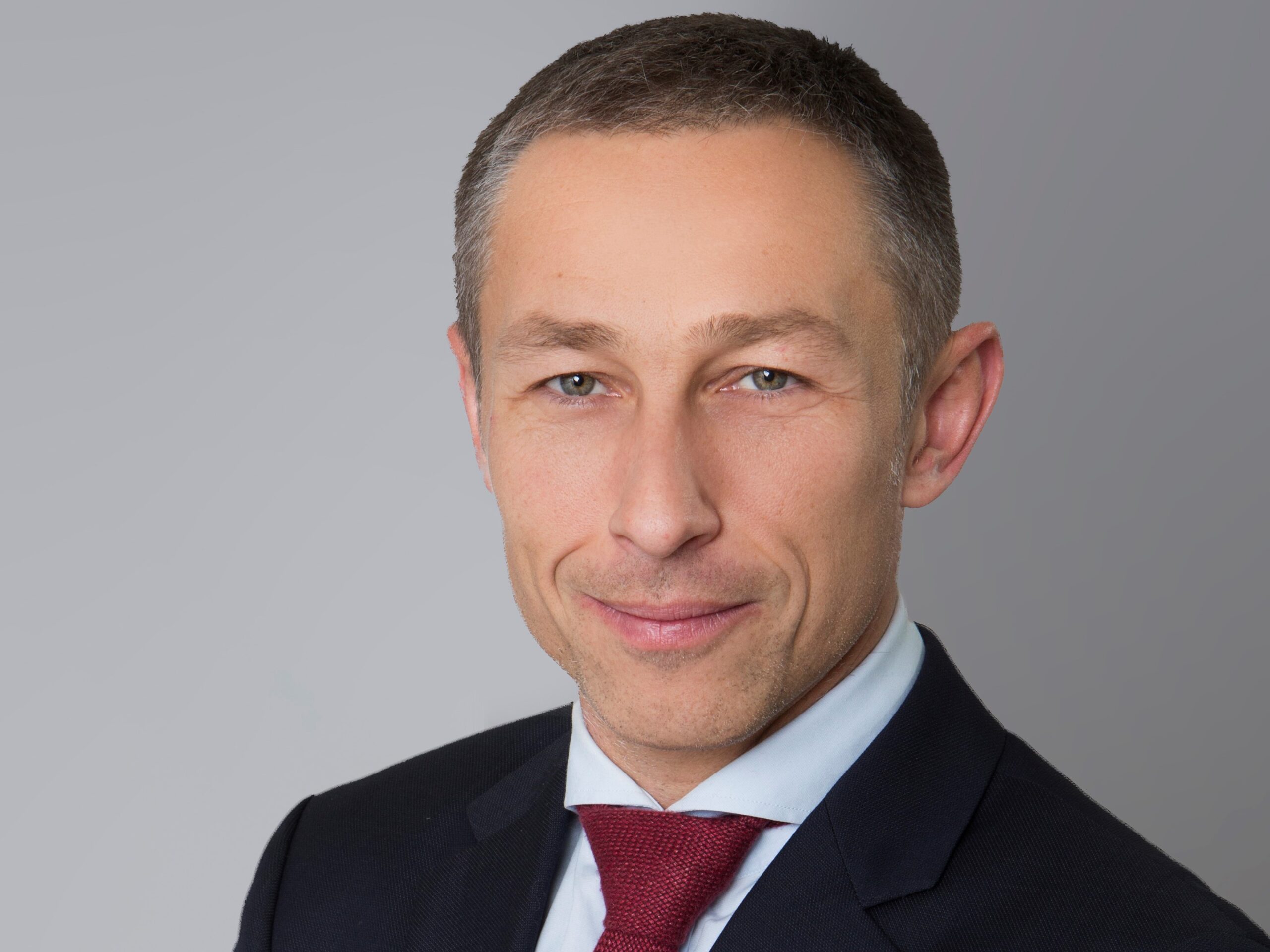
Beton może być piękny
Zdobyte w ciągu 10 lat doświadczenie pozwoliło Kroe zbudować w Polsce zapotrzebowanie na fasadowe płyty betonowe GRC, które tworzone na specjalne zamówienie pozwalają podkreślać unikatowość i niepowtarzalność inwestycji. Gdzie można podziwiać te perełki architektoniczne, a także jak wygląda proces ich powstawania? O tym opowiada ŁUKASZ ŻYŁA, Prezes Kroe, w rozmowie z Natalią Chylińską.
Natalia Chylińska: Betonowe żyletki – tak określa się wyjątkowe prefabrykaty na elewacji .KTW, które wyszły spod ręki specjalistów Kroe. Jaka była droga dochodzenia do takiego efektu?
Łukasz Żyła: Architekci rozrysowali kilka koncepcji, a my przygotowaliśmy próbki z uwzględnieniem wszystkich wytycznych technicznych. Po wyborze docelowego wzoru wykonaliśmy mock-up w skali 1:1. Co ciekawe, panel został powieszony przed wejściem do siedziby Medusa Group, gdzie wisiał kilkanaście miesięcy. Dzięki temu można było zaobserwować, jak zmienia wygląd przy oddziaływaniu czynników atmosferycznych.
N.Ch.: Sprostaliście wyzwaniu przy .KTW I. Czy dzięki temu przy .KTW II te prace przebiegały dużo szybciej?
Ł.Ż.: Z jednej strony było łatwiej, bo wiedzieliśmy, jaka płyta jest potrzebna, ale okazało się, że inwestor narzucił dużo większe tempo. Musieliśmy wykonywać 150 paneli tygodniowo, co całkowicie obciążało naszą produkcję. Dostarczaliśmy je z Krakowa, gdzie jest nasz zakład, nie do Katowic, lecz aż pod Poznań. Tam były montowane w aluminiową ramę ze szkłem i izolacją. Dzięki temu montaż na budowie przebiegał dużo sprawniej. To wyzwanie było przełomowym momentem w rozwoju Kroe. Zapadły decyzje o rozbudowie produkcji, abyśmy równolegle mogli pracować nad 3–4 inwestycjami, a nie tylko jedną. Zaczynaliśmy od małych, prywatnych projektów. Doszliśmy do największych w kraju realizacji publicznych. Nasze zdolności produkcyjne fasad betonowych GRC utrzymują się na poziomie 25 tys. m2 rocznie.
N.Ch.: Wszystkie prefabrykaty produkowane przez Kroe są tworzone pod specjalne potrzeby danego obiektu. Jakie inne elewacje zasilają portfolio firmy?
Ł.Ż.: Od 10 lat działamy na rynku w Polsce, ale mamy już także wypracowane pozycje w Londynie, Holandii czy Szwajcarii. Dlatego możemy pochwalić się udziałem w budowie najwyższego w Europie budynku modułowego. Myślę tu o Domu Akademickim w Croydon w Londynie. Wykonywaliśmy tam przestrzenne portale drzwiowe. Warto wspomnieć też o budynku Canalside Walk przy Paddington Basin w Londynie, gdzie dostarczyliśmy panele 3D w rozmiarach 3,5 x 2 m w kolorze kamienia portlandzkiego. Jeśli chodzi o rodzimy rynek, to oprócz .KTW braliśmy udział w budowie Archiwum Narodowego w Krakowie czy Muzeum Wojska Polskiego.
Elewacja .KTW Dom Akademicki w Croydon w Londynie Podium Park
N.Ch.: Beton to nie jedynie element elewacji. Często wykorzystywany jest także wewnątrz obiektów.
Ł.Ż.: Dla dwóch budynków inwestycji Podium Park w Krakowie wykonaliśmy płyty okładzinowe dla holi windowych na 10 kondygnacjach oraz okładziny dla holu głównego i lobby z płytami zawierającymi logo. Celem było osiągnięcie podobieństwa do piaskowca. Ze względu na aspirację otrzymania certyfikatu BREEAM Excellent wymagano stosowania materiałów o niskim śladzie węglowym. Dlatego odchudziliśmy nieco płyty, aby zużyć mniej surowców. Warto tu podkreślić, że beton GRC jest bardzo ekologiczny, produkowany z naturalnych surowców, w 100% podlega recyklingowi. Wracając jeszcze do tematu wnętrz z naszym udziałem, to do Varso Tower realizowaliśmy ogromne panele o powierzchni ok. 7–8 m2 ze strukturą, piaskowane, zaprojektowane przez Normana Fostera, znanego architekta z londyńskiej pracowni Foster and Partners.
N.Ch.: Każde zlecenie wiąże się z realizowaniem pomysłów od podstaw i robieniem czegoś, czego nikt wcześniej nie robił. Ciekawi mnie, jak technologicznie udaje się temu sprostać. Sukces tkwi w ludziach, ich wiedzy i chęci eksperymentowania? A może to tylko kilka z wielu czynników?
Ł.Ż.: Dokładnie – na sukces składa się wiele elementów. Niezaprzeczalnym atutem Kroe jest młody i ambitny zespół. To architekci, więc potrafią zrozumieć wizję innych projektantów. Wspierają ich technolodzy swoją wiedzą oraz artyści realizujący koncepcję. Dysponujemy doświadczoną kadrą technologów, a wdrożone procedury zakładowej kontroli produkcji, własne laboratorium oraz praca na atestowanych surowcach pochodzących od najlepszych dostawców dają gwarancję jakości i dokładności wykonania. Jest to corocznie potwierdzone rygorystycznym audytem członkostwa w Międzynarodowym Stowarzyszeniu Producentów GRC, do którego należy zaledwie ok. 20 firm z całego świata kierujących się najwyższymi światowymi standardami.
Reżim technologiczny wymagany przy produkcji natryskiwanego GRC jest tak wysoki, gdyż to od niego zależy bezpieczeństwo i życie ludzi – panele fasadowe, zwłaszcza formowane elementy 3D, potrafią mierzyć kilkanaście m2 w rozwinięciu i ważyć kilkaset kilogramów przy grubości 15–30 mm. Tego nie może zagwarantować przypadkowy producent.
Jesteśmy przygotowani do wsparcia projektu na etapie rozwiązań fasady poprzez pracę z architektami nad wyborem kolorów, faktur, wykończenia powierzchni, aż do sposobów zamocowań, logistyki produkcji, dostaw oraz pełnej obsługi w zakresie wymaganej dokumentacji projektowej, technicznej czy technologicznej. Wdrożyliśmy systemy zarządzania ISO 9001 oraz ISO 14001, a wiedzę o materiale poszerzamy, współpracując z uczelniami technicznymi.
N.Ch.: W betonie widzi Pan więcej niż inni. Skąd wzięło się to zamiłowanie
i pomysł na takie ukierunkowanie działalności firmy?
Ł.Ż.: Z betonem jestem związany od dziecka – za sprawą rodzinnej firmy. Praca w branży betonu towarowego pozwoliła mi poznać ten materiał, a zainteresowanie rozwojem nowych technologii betonowych skierowało uwagę na GRC. Ten materiał całkowicie mnie zafascynował – postanowiliśmy pokazać, że beton oprócz wszystkich swoich zalet ma jeszcze jedną – może być piękny! Dla świata nie jest to jedynie materiał konstrukcyjny. Postanowiłem to zakrzewić na polskim rynku. Była to trudna droga, bo wchodziliśmy na rynek z produktem, którego nikt nie potrzebował i nie oczekiwał, bo zwyczajnie nie znał.
Staramy się zainteresować architektów możliwościami tego materiału. A jest ich wiele i czasami wymagają całkowitej zmiany dotychczasowego sposobu myślenia. Fasady wykonane w technologii GRC są wytrzymalsze niż konkurencyjne materiały na rynku. Trwałość fasad betonowych określa się na 50 lat, a koszty konserwacji w długim okresie są na znacznie niższym poziomie. Co więcej, materiał ten starzeje się z charakterem, dzięki czemu zachowuje walory estetyczne.
Fot. arch. TDJ Estate